4방향 스트레치 의류 직물을 의류로 가공하려면 성공적인 제조와 최종 제품의 원하는 성능 특성을 보장하기 위해 몇 가지 준비가 필요합니다. 프로세스와 관련된 주요 준비 사항은 다음과 같습니다.
직물 검사: 가공 전, 4방향 스트레치 원단 재료의 결함이나 결함을 식별하기 위해 철저한 검사를 거칩니다. 여기에는 고르지 않은 늘어짐, 직물 뒤틀림, 직조 또는 편직 구조의 불규칙성을 확인하는 것이 포함됩니다. 발견된 결함은 의류 생산 과정에서 수정 또는 절단을 위해 표시됩니다.
패턴 레이아웃 및 커팅: 패브릭은 커팅 테이블에 배치되고 의류 패턴은 패브릭 사용을 최적화하고 낭비를 최소화하기 위해 신중하게 배치됩니다. 최종 의류의 적절한 핏과 성능을 보장하기 위해 원단의 신축 방향에 특별한 주의를 기울입니다. 절단은 깨끗하고 정밀한 가장자리를 얻기 위해 날카로운 회전 블레이드 또는 컴퓨터 절단기를 사용하여 수행됩니다.
솔기 준비: 원단의 신축성을 고려하여 솔기 제작 시 특별한 고려 사항이 적용됩니다. 직물의 신축성을 수용하기 위해 솔기 여유분을 조정해야 할 수 있으며, 신축성 스티치, 서징 또는 플랫록 솔기와 같은 기술을 사용하여 착용 중 솔기 주름이나 파손을 방지합니다.
실 선택: 신축성 있는 원단에 적합한 고품질 실을 선택하여 스티칭합니다. 신축성이 있는 폴리에스테르나 나일론 실은 직물의 신축성 특성에 맞는 솔기 내구성과 탄력성을 보장하기 위해 일반적으로 사용됩니다.
장비 설정: 신축성 있는 직물을 적절하게 처리할 수 있도록 재봉틀과 서저를 조정하고 보정합니다. 여기에는 재봉 중 스티치 건너뛰기, 실 끊김 또는 천 뒤틀림을 방지하기 위해 스티치 장력, 바늘 유형 및 기계 설정을 미세 조정하는 작업이 포함될 수 있습니다.
테스트 및 프로토타입 제작: 본격적인 생산에 앞서 핏, 기능성, 내구성을 테스트하기 위해 4방향 스트레치 원단을 사용하여 샘플 의류 또는 프로토타입을 만드는 경우가 많습니다. 이를 통해 최종 의류가 품질 표준을 충족할 수 있도록 패턴이나 제작 기술에 필요한 조정이 가능합니다.
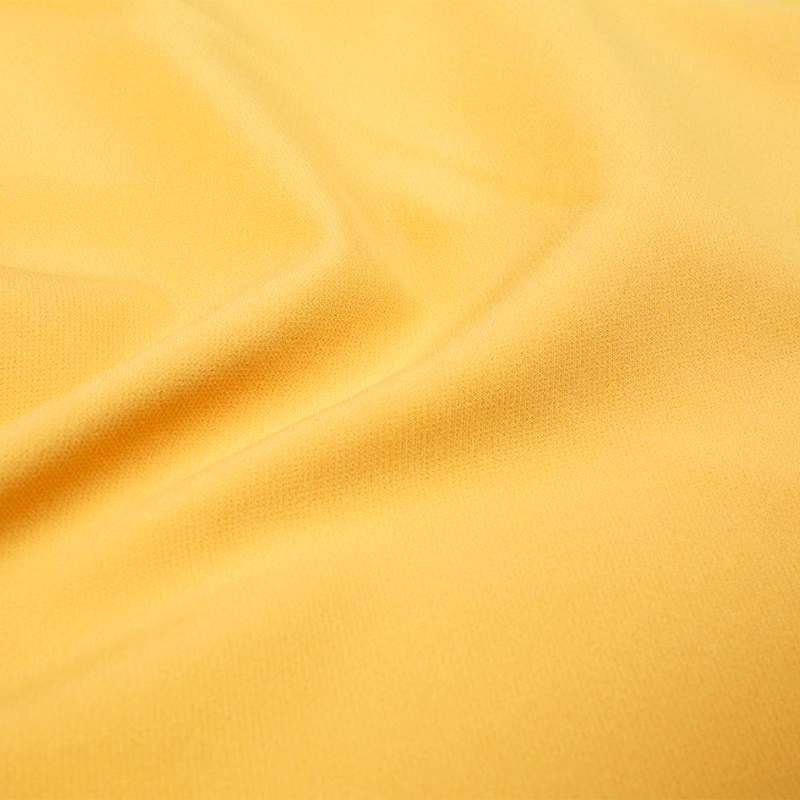
특수 기술: 의류의 디자인과 용도에 따라 성능과 편안함을 향상시키기 위해 특수 제작 기술이 사용될 수 있습니다. 여기에는 응력 지점에 보강재를 통합하거나, 수분 흡수 또는 항균 처리를 추가하거나, 부피를 줄이고 미적 개선을 위해 열 밀봉 또는 접합 솔기를 적용하는 것이 포함될 수 있습니다.
품질 관리 조치: 의류 생산 공정 전반에 걸쳐 일관성을 유지하고 사양 준수를 보장하기 위해 엄격한 품질 관리 조치가 구현됩니다. 여기에는 절단된 조각의 정확성 검사, 재봉 중 솔기 무결성 모니터링, 완성된 의류에 결함이 있는지 최종 검사 수행이 포함됩니다.
마무리 손질:의류를 함께 꿰매고 나면 여분의 실을 다듬고 밑단 감기, 라벨 부착, 잠금 장치나 장식 추가 등의 마무리 손질이 완료됩니다. 의류는 포장하기 전에 광택 있는 외관을 보장하기 위해 최종 프레싱 또는 스팀 처리를 거칠 수도 있습니다.
포장 및 라벨링:완성된 의류는 특정 요구 사항에 따라 조심스럽게 접거나 걸고 포장됩니다. 규제 표준 및 고객 선호도에 따라 의류 관리 지침, 사이즈 정보 및 브랜드가 포함된 라벨이 부착되어 있습니다.